How ERW Pipe Mills Revolutionize Pipe Manufacturing Processes
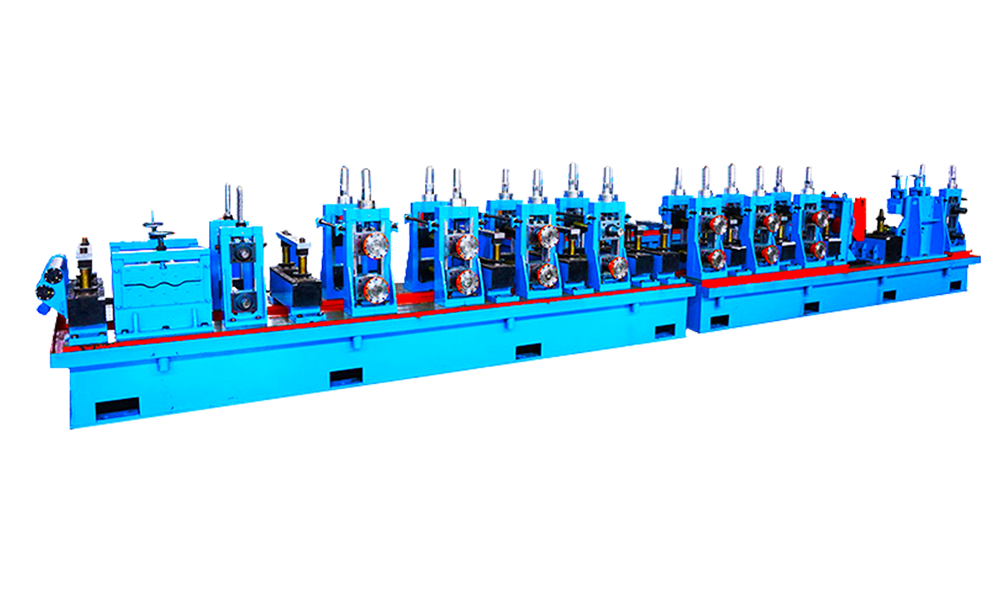
Electric Resistance Welding (ERW) pipe mills have brought a significant transformation to the pipe manufacturing industry. By leveraging advanced technology, these mills have streamlined production, enhanced product quality, and reduced costs. This article delves into how ERW pipe mills have revolutionized the manufacturing processes and what makes them a game-changer in the industry.
What Are ERW Pipe Mills?
ERW pipe mills are specialized facilities where pipes are manufactured using the electric resistance welding process. This process involves forming a flat steel strip into a cylindrical shape and welding its edges together without the use of filler materials. The result is a seamless and robust pipe suitable for various applications, including water distribution, oil and gas transportation, construction, and more.
Key Advantages of ERW Pipe Mills
1. High Efficiency
ERW pipe mills are designed for continuous production, allowing for higher output rates compared to traditional methods. The automated systems ensure consistent operation with minimal downtime, enabling manufacturers to meet high demand efficiently.
2. Precision and Uniformity
Advanced technology in ERW pipe mills ensures precise control over dimensions, wall thickness, and weld quality. This uniformity is crucial for industries requiring exact specifications, such as the oil and gas sector.
3. Cost-Effectiveness
The electric resistance welding process eliminates the need for additional materials like welding rods or flux. Combined with high production speeds, this reduces manufacturing costs significantly, making ERW pipes a cost-effective solution.
4. Environmentally Friendly
ERW pipe mills produce less waste compared to other methods, as the process utilizes a continuous strip of steel. Additionally, the absence of filler materials reduces environmental impact, aligning with sustainable manufacturing practices.
How ERW Pipe Mills Enhance the Manufacturing Process
Advanced Automation
Modern ERW pipe mills employ automated systems for every stage of production, from forming and welding to cutting and inspection. This reduces the likelihood of human error, ensuring consistent quality and efficiency.
Inline Inspection and Testing
ERW pipe mills incorporate real-time inspection technologies, such as ultrasonic and radiographic testing, to ensure weld integrity and pipe quality. These inline testing methods help identify and address defects immediately, maintaining high standards.
Versatility in Production
ERW pipe mills can produce pipes of various sizes and thicknesses, catering to a wide range of applications. The flexibility to switch between specifications quickly makes these mills adaptable to diverse market demands.
Applications of ERW Pipes
ERW pipes manufactured in these mills are widely used across industries due to their strength, reliability, and affordability. Key applications include:
- Oil and Gas Transmission: Used for transporting oil, gas, and other hydrocarbons over long distances.
- Water Supply: Employed in municipal and industrial water distribution systems.
- Structural Use: Utilized in construction projects for scaffolding, building frameworks, and infrastructure.
- Automotive Industry: Integrated into vehicle designs for components such as axles and chassis.
Challenges and Innovations
While ERW pipe mills have revolutionized manufacturing, they face challenges like maintaining weld quality at high speeds and adapting to new materials. However, ongoing innovations in automation, machine learning, and material science continue to address these issues, ensuring the technology evolves to meet future demands.
Conclusion
ERW pipe mills have redefined the pipe manufacturing industry by offering a combination of efficiency, precision, and cost savings. Their ability to produce high-quality pipes for diverse applications makes them an indispensable part of modern industrial infrastructure. As technology continues to advance, ERW pipe mills will undoubtedly play a pivotal role in shaping the future of manufacturing processes.