Cutting-Edge Steel and Beyond Every Modern Metal Fabricator Should Know
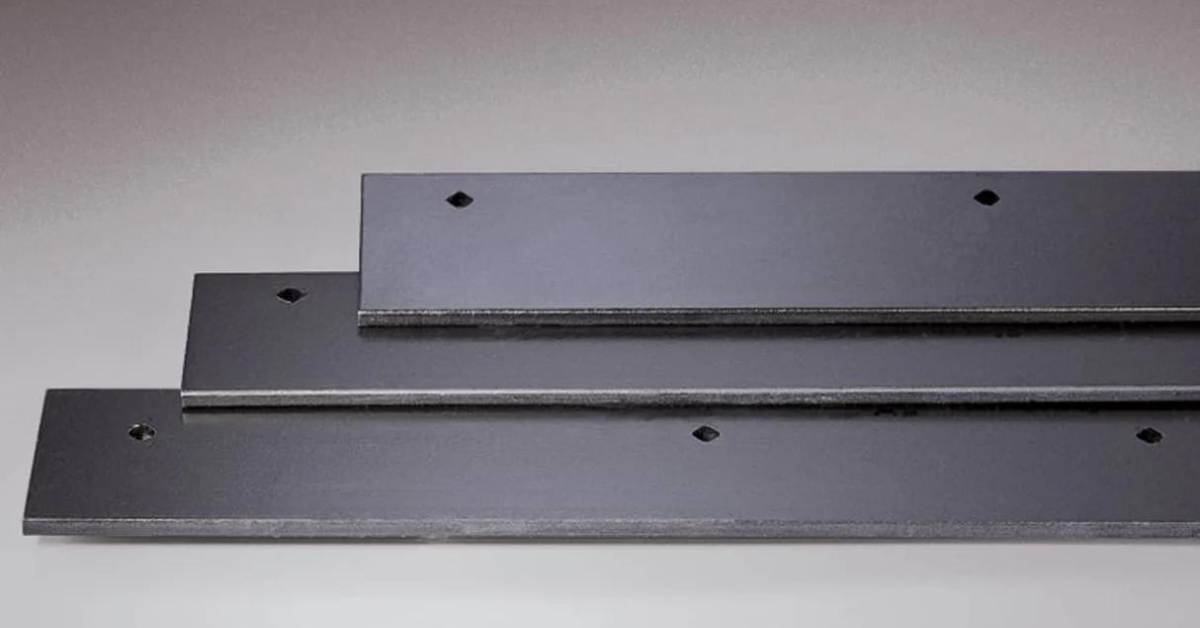
In the fast-paced world of metal fabrication, innovation is key to staying competitive. This blog post examines new techniques and technologies that are transforming the industry, offering valuable insights for both experienced professionals and newcomers. Understanding these advancements can lead to exciting opportunities in the field.
Evolution of Metal Fabrication Techniques
Metal fabrication has come a long way from its humble beginnings. Traditional techniques, such as casting and forging, laid the groundwork for the industry. These methods, while effective, were limited by their reliance on manual labor and time-consuming processes. However, with the advent of technology, the industry has witnessed a monumental shift towards precision and efficiency.
One of the significant advancements is the introduction of computer numerical control (CNC) machines. These machines revolutionized the industry by allowing for automated, high-precision fabrication. With CNC, complex designs can be executed with remarkable accuracy, reducing human error and increasing production rates. Laser cutting further enhanced precision, enabling fabricators to create intricate patterns and designs with ease.
Another leap forward came with the development of additive manufacturing, commonly known as 3D printing. This technique allows for the creation of complex structures layer by layer, offering unparalleled design flexibility. Metal 3D printing, in particular, has gained traction, providing fabricators with the ability to produce lightweight, robust components that were previously impossible to achieve through traditional methods. Additionally, blasting services can complement this technology by preparing surfaces for optimal adhesion and performance.
Exploring Key Technologies Impacting Metal Fabrication
Several key technologies are transforming the metal fabrication industry, each offering unique advantages and challenges. One such technology is robotics. Robots equipped with advanced sensors and artificial intelligence are now capable of performing intricate tasks with incredible precision. They can handle repetitive tasks, such as welding and assembly, with unmatched consistency, improving both efficiency and safety in the workplace.
In addition to robotics, digital twins are making waves in the industry. Digital twins are virtual replicas of physical objects that allow engineers and fabricators to simulate various scenarios before actual implementation. By using digital twins, manufacturers can optimize designs, identify potential flaws, and reduce the need for costly prototypes.
Another game-changer is the integration of the Internet of Things (IoT). IoT devices can collect real-time data from machines and equipment, providing valuable insights into production processes. This data-driven approach enables predictive maintenance, reducing downtime and improving overall productivity. With IoT, fabricators can monitor and control operations remotely, enhancing flexibility and responsiveness.
Predicting the Future of Metal Fabrication
Looking ahead, the future of metal fabrication is brimming with potential. One of the most promising trends is the continued integration of artificial intelligence (AI) and machine learning. AI can optimize production schedules, improve quality control, and enhance decision-making processes. By analyzing vast amounts of data, AI algorithms can identify patterns and suggest improvements, driving efficiency and innovation.
Sustainability is also expected to play a significant role in the industry’s future. As environmental concerns grow, fabricators are exploring eco-friendly materials and processes. Recycling and reusing metals, as well as adopting cleaner energy sources, are becoming integral parts of sustainable fabrication practices. By reducing waste and emissions, the industry can contribute to a greener future.
Additionally, collaborative robots, or cobots, are set to become more prevalent in metal fabrication. Cobots work alongside human operators, assisting with tasks that require both precision and adaptability. This synergy between humans and machines not only enhances productivity but also opens up new possibilities for creativity and innovation.
Read Also: Cataz Net: The Future of Online Streaming
Conclusion
In conclusion, innovation is the lifeblood of the metal fabrication industry. From the evolution of traditional techniques to the integration of cutting-edge technologies, fabricators have continuously pushed the boundaries of what is possible. By staying informed about these advancements, professionals can harness the power of innovation to drive efficiency, quality, and sustainability in their operations.